QUALITY, BESPOKE AND LONG LASTING
CONTRACT FURNITURE
We have a clear process for each order to make sure no detail is overlooked and every piece of furniture is completed to the highest standard.
Every stage of this process is managed by our experts:
SALES & PROJECT MANAGERS
Gather your initial details to get a comprehensive understanding of your needs. Your dedicated point of contact.
DESIGN TEAM
Put together the design ideas and produce CAD drawings to give you a clear understanding of the bespoke products.
JOINERY EXPERTS
Build the frames in-house, paying close attention to detail and measurements to make sure everything fits together perfectly.
SPRAY TEAM
Any timber and even metal components are then finished to suit the design. Find out more about our spray services.
UPHOLSTERY TEAM
Bring the initial designs to life, by using the material picked out to upholster the seating.
INSTALLATION
Deliver and fit the final furnishings in place, to the highest standard.
OUR TEAM
We have a team with years of experience, renowned for our quality and service, we will work with you to produce an exceptional result.
WHAT SETS ATLAS CONTRACT
FURNITURE APART:
LIMITLESS CUSTOMISATION OPTIONS
Our made to measure service offers endless tailoring options that means each piece of furniture is truly bespoke. Our in-house production team provide expert care and precision at every step of manufacturing, ensuring outstanding quality.
EXCEPTIONAL LEVEL OF DETAIL
We pride ourselves on delivering quotes and drawings with a high level of detail to provide answers for the most complex questions and ensure clarity at all stages of the project.
WORLDWIDE DELIVERY & INSTALLATION
We provide a global service, having served clients worldwide and installed bespoke seating in venues across the UK and beyond. We work closely with international clients to ensure we find the best economical solution for the project.
NO PROJECT IS TOO BIG OR SMALL
Our work ranges from large scale installations with multiple units of intricately designed furniture, to projects requiring just one piece of standout seating. Our level of service remains the same across any project size.
SEATING SOLUTIONS
THAT REFLECT YOUR INDIVIDUAL NEEDS
All aspects of our banquette bench seating can be fully customised to suit your requirements. Our mission is to create outstanding seating solutions that reflect each client’s individual needs and style. Visit our Seating design pages for a range of popular styles and options.
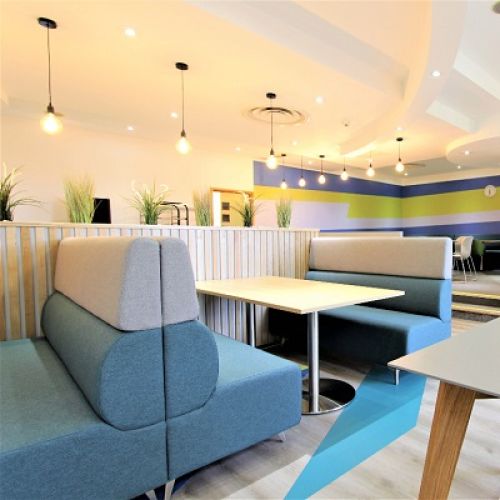
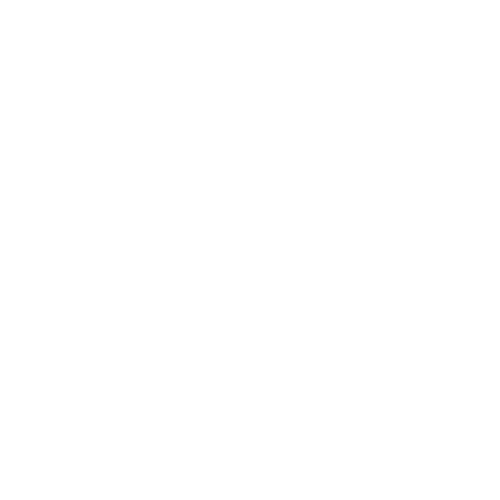
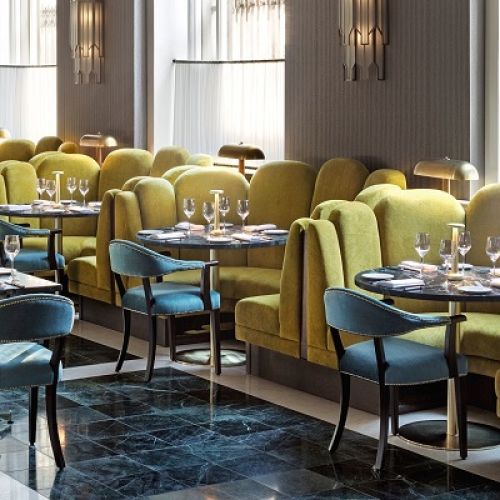
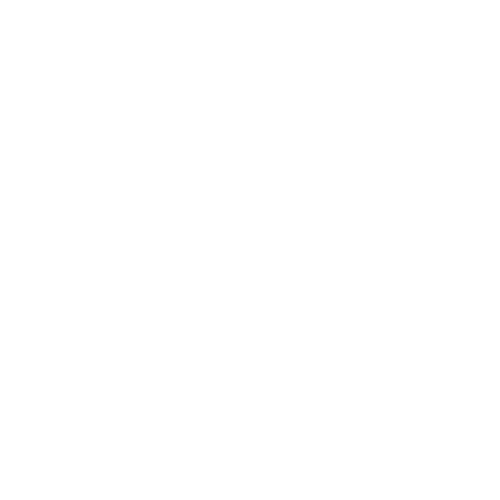
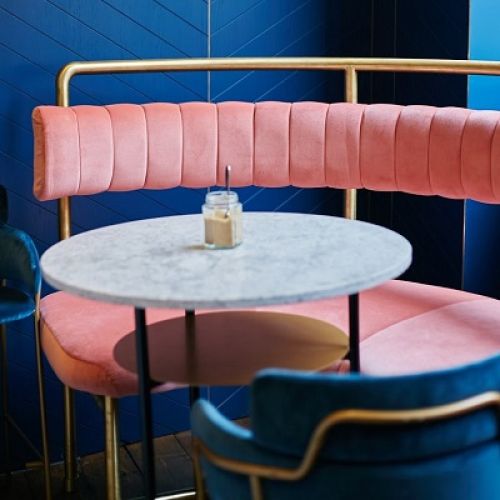
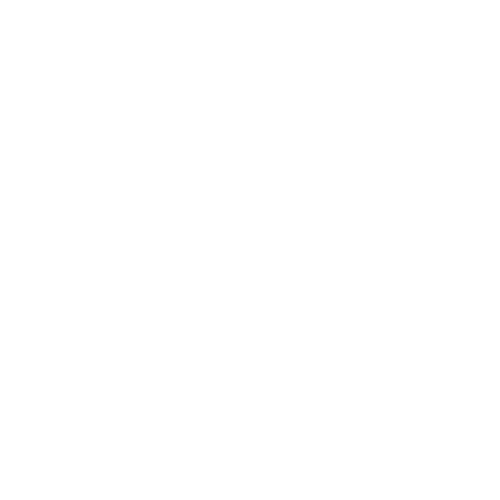
Contact Us Today
Whether you have general questions or if you have your measurements and designs ready to get a quote, our experiences team are happy to assist you and discuss your next project. Get in touch by phone, email, or our enquiry form today.